Technical Column
What is EDM? Advantages, disadvantages, and accuracy.
This article explains electric discharge machining (EDM).
We will introduce not only the advantages but also the disadvantages, so please check the article.
Contents
What is EDM?
This is a method of processing metal by causing electrical sparks between the electrode and the workpiece in a processing fluid (water or oil) and melting the metal with its heat.
It is possible to precisely machine complex shapes even on hard metals that cannot be machined by normal cutting.
Advantages of EDM
The following are four electric discharge machining advantages.
1. High-precision machining of complex shapes
Even complicated shapes that are difficult to manufacture by grinding
can be machined with high-precision machining.
2. Materials with high hardness can be processed
Even extremely hard materials with difficulty of grinding such as cemented carbide
can be processed using this method.
3. No deformation due to heat
EDM is performed in machining fluid, which cools down the materials.
So there is no thermal deformation.
4. No burrs occur
No burrs are produced during the cutting process, which reduces the need for deburring.
Disadvantages of EDM
On the other hand, electric discharge machining has the following disadvantages.
1. Conductivity is required
Since the material is processed using electricity,it is not possible to process non-conductive materials.
2. Processing time is long
The work piece is gradually melted by electrical discharge, which takes a long time.
3. Electrodes need to be prepared
In die-sinking EDM process, the workpiece is processed into the shape of the electrode, therefore it is necessary to prepare for the electrode according to the desired shape.
4. The direction of processing is limited
In WEDM, the direction of the wire is fixed vertically, limiting the direction of machining.
5. A heat-affected layer different from the grinding process will form.
Due to the rapid temperature rise and solidification of a EDMed surface, a heat-affected layer is formed as shown in Fig. 1, which is clearly different from the grinding process.
The heat affected layer of a cemented carbide has lower mechanical performance than the base metal, and can have defects like cracks.
It is recommended to remove it as much as possible by finishing.
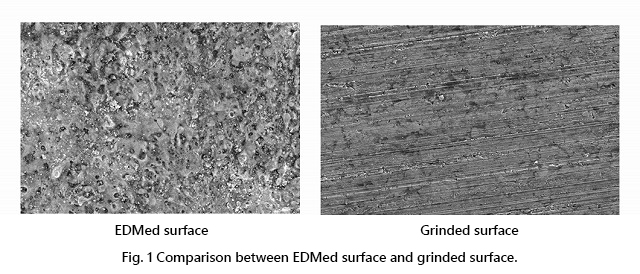
Materials suitable for EDM
Materials suitable for electric discharge machining are conductive materials that are difficult to cut due to their high hardness such as cemented carbide.
In terms of cemented carbide grades, the grades with coarse particle sizes are more suitable as growth of microcracks generated during EDM could be blocked by coarse particles.
Fig. 2 shows the transverse rupture strength measurement results of medium particle carbide and fine particle carbide after grinding and EDM. The reduction rate of transverse rupture strength after EDM is lower for medium particle carbide than the fine particle carbide.
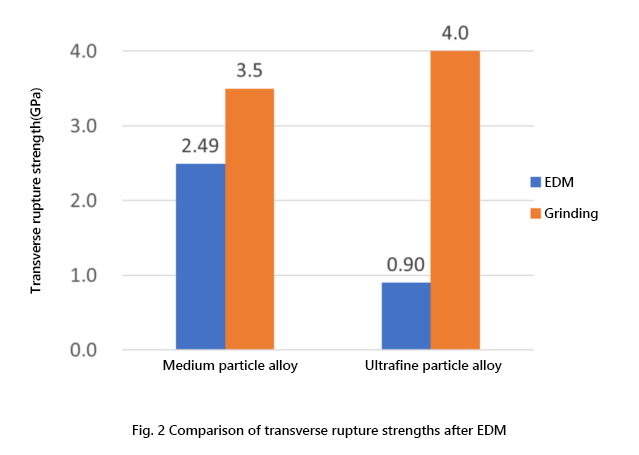
In addition, there is no problem in oil, but when processing in water, corrosion as shown in Fig. 3 may occur.
So, when processing in water for a long time, grades containing corrosion resistant ingredients are suitable.
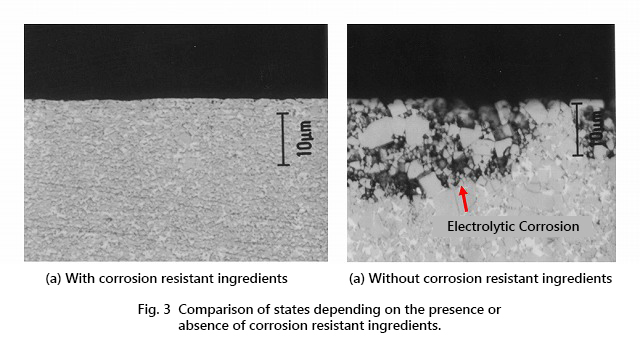
Precision of EDM
As mentioned above, high-precision machining can be achieved by EDM.
The following is a reference of the precision that could be achieved, and may depend on product size and specification:
WEDM:
Dimensions / ± 0.002 mm Position / ± 0.002 mm Surface roughness (RZ) /0.8
EDM:
Dimensions / ± 0.003 mm Position / ± 0.003 mm Surface roughness (RZ) /1.5
Small hole EDM:
Dimensions / ± 0.005 mm Position / ± 0.003 mm Surface roughness (RZ) / 3
We will handle it
We have the know-how to analyse and investigate the wear and deterioration of cemented carbide moulds and toolings, identify the causes of defects from the results, and propose the most suitable machining method for the identified causes, based on past experience of improvement cases and theoretical perspectives.
If you have any concerns about materials or processing methods, please feel free to contact us.
-
Catalog
We will provide high value-added cemented carbide with the achievements and know-how cultivated so far.
Download -
Consultation and Inquiry
We solve your problems by providing integrated solutions from material selection/development to precision machining and provision of finished products.
Contact us -
FAQ
We have posted the contents of many inquiries from customers in the past.
Click for details